Ihab Saad – Developing the schedule
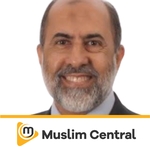
AI: Summary ©
The speakers discuss the importance of identifying and breaking down a project to determine the activities needed to achieve the project. They stress the need for clear distinction in order to avoid delays and consider resource and technology constraints when scheduling a project. The process of identifying and breaking down the project involves identifying and breaking down each activity and identifying and breaking down the project for each classifications. The speakers also discuss the use of technology and the constraints surrounding the project, including logistical, political, and cultural constraints. They outline the process of breaking down the project for each activity and identifying and breaking down the project for each classifications. The importance of finding the right duration for each activity and using productivity tables to estimate the work test duration is emphasized.
AI: Summary ©
Hello. Today, we're going to learn about building the schedule. What
do we mean by building the schedule, and how to break down a
big project into smaller components, along which lines and
how many activities should a project have, and so on and so
forth. So basically, what we're going to discuss is how to
identify the activities in a project, how to determine the
activity durations and the relationships among the activities
and linking them and so on. This is going to be a review of what we
learned before about the different types of relationships and so on.
But we're going to talk primarily about the first task in schedule
development, which is activity definition, how to break down the
project into activities.
So construction planning can be either cost oriented or schedule
oriented. And to give an example on that, the cost oriented is
going to look at the direct costs and the indirect costs. The direct
costs are basically costs involved directly in the construction
operation on site, whereas indirect costs are going to be
costs needed to be spent on the project, but not necessarily
related to any particular activity. So for example, if you
have
a central purchasing department at the headquarters of the company.
This purchasing department is working on all projects or any
scheduling department, or any Central Department, the legal
department, for example, you cannot pinpoint and say they work
that long on this particular project or that project. So it's
going to be a general overhead for the head office, whereas direct
costs are going to be the cost of the people assigned to the
construction site, field engineers, Superintendent, project
manager, etc. When we look at the time aspect of the project, the
schedule oriented idea, we have time oriented, which is going to
be developing the critical path of the project and resource oriented
which is going to be, what kind of resources do we need? When are we
going to need them in what amount, and so on and so forth.
This resource oriented planning is going to be sort of joint between
the schedule oriented planning and the cost oriented planning,
because, again, every resource has its own cost, so we need to
calculate the cost of these resources as well.
Before starting our scheduling effort, we have to read the
specifications and the plans, because, for example, the general
conditions of the contract are going to have an effect on the
selection of the activity and the sequencing of the activities and
the responsibilities and so on and so forth. The staffing of the
project, of course, is going to be also contingent upon, upon these
plans and specs, choosing the appropriate technology, what kind
of technology is going to be available in the project, location
and affordable to the company that's going to be undertaking
that project, identifying and listing activities. How are we
going to break down a huge elephant like the project into
more manageable tasks or activities the size of an ant
compared to that elephant, and then calculating the activity
durations based on the resources that are going to be identified
for each activity and the resource availability, whether it's whether
it's money or materials, equipment, subcontractors, etc,
and labor, identifying the relationships between activities.
So which activity comes first, what's going to be the predecessor
to what, what's going to be a successor to what, which two
activities can be done at the same time, and what kinds of lags and
overlaps, what's what kinds of constraints are going to govern
the relationship between activities? All of that has to be
involved. And then, once we identify the relationships, after
breaking down the project into activities. We have to link these
activities, and once we have linked them, now we're going to
add the durations that we have already calculated to calculate
the activity times and the project duration based on the algorithm of
the critical path that we have already learned about, early
start, early finish, late start, late finish, total and free float,
which are going to be calculated from the forward pass, the
backward pass and determining the critical path of the project.
When we talk about the choice of technology, it's the choices of
appropriate of appropriate technology and methods for
construction which sometimes are often ill structured yet critical
ingredients in the success of the project. So if we do not have a
clear structuring of when are we going to need this piece of
equipment, we might end up acquiring it too early, which is
going to result in additional cost, or too late, which might
result.
In a delay to the project. Same thing applies to the materials. If
there's a shortage of that material, we have to order it in
advance. It might be a long lead item that needs a long time to
manufacture or to get ready for delivery to the construction site.
So we have to plan for the cost of storage and storage conditions and
so on and so forth. Or are we going to the to rely on just in
time delivery to the construction site at the time when the activity
is going to be performed, therefore not needing any storage.
Of course, the danger with just in time planning is that if you need
it right now and it's not delivered right now, that means
that you're going to have a delay. We need to consider the
constraints of the site and the influence of selected technology
on schedule and cost. So again, constraints of the site could be
either logistical constraints like access to the site, for example,
it could be political constraints. It could be other
other constraints that might affect the site. So weather
constraints, for example, maybe there are some activities that
have to be done in a dry environment. So if it rains, we
cannot perform them. The tower train should not be working when
the wind speed exceeds a certain speed, and things like that. So
we're going to look at the meteorological reports from
previous years to try to identify what are the constraints that are
going to be imposed on our construction activities,
to identify the list activities. Activities represent the necessary
framework to permit scheduling, along with estimating the
resources required by the individual activities. So we
again, that's why we need to have clear distinction. What is this
activity, what amount of work is going to be associated with that
activity? What kind of resources are going to be needed in what
amount and what's the cost of these resources, what's the
production rate of these resources? All of these details
are got to be required for each activity that's gone. That's why
we might end up having having something like a an activity form
that shows the name of the activity, its location, who's
responsible for it, what kind of resources are going to be
involved? What are the rates of application, or rates or for
performance of these resources? And that leads, at the end to the
duration of the activity and the cost of the activity.
The set of activities defined for a project should be comprehensive,
but not too refined, because, again, there's a very high
likelihood that we might end up adding activities or consolidating
some other activities. So basically, we're going to think
creatively based on our experience. How did we do it in
the past? And we're gonna develop a set of activities. But again,
have an open mind for the possibility of adding additional
activities if, for example, the activity duration exceeds, let's
say, a couple of weeks, maybe we need to break it down into two. Or
if the duration of the activity is less than one day. Maybe we need
to consolidate it with another activity to be more meaningful.
Construction plans can easily range between less than 100
activities to several 1000 defined tasks. And again, we are usually
going to start with a very summarized schedule, or collapsed
schedule, that's going to have the main milestones. When do I need to
start work, the notice to proceed. When do I need to finish the
underground work? When do I need to finish the skeleton, the
topping off of a steel structure, or the completion of the concrete
structure, for example? When do I need to have enclosed the building
to start the dry work inside the building and so on and so forth?
When is going to be my substantial completion? When it's going to be
my final completion? So we are identifying major milestones in
the project, and that's going to be my main initial schedule. And
then I'm going to fill in the blanks, so this is like a
skeleton, and then I'm going to add the flesh and the skin and all
the other details to that schedule.
Typically, each design element in the plant facility will have one
or more associated project activities. So the foundations are
going to have probably more than one activity. The walls are going
to have more than one activity. The HVAC AC system is going to
have more than one activity, and so on and so forth. Those
activities will involve different resources, or those activities
that do not require continuous the two types, two major types here,
activities that involve different resources, like any production
activity, for example, or any procurement activity, and those
activities that do not require any continuous performance, like
submittals, one of the activities is to submit a sample to the
Arctic engineer for review and approval or reviews. We're going
to have a review of a certain document, or we're going to have
an inspection.
Or something like that.
Building Element Classification can be used as a guidance to list
group major building activities. So we're going to have
foundations, superstructure, mechanical system, electrical
system, etc. These could be major classifications under which I'm
going to break them down into smaller entities until I reach the
level of activities. So here, for example, is one of the formats.
It's called the Uniformat, and it's sometimes used in estimating
and embedding as well as in scheduling. So here, for example,
we have the structure, the substructure, the shell interiors,
services, etc, and each one of them shows
little bit more level of detail. So the substructure is going to
have foundations and basement construction. It could also
include any infrastructure, utilities, pipes, cables, etc. And
then we can break it down even further into standard Foundation,
special foundations, slab on grade, basement excavation,
basement walls and so on. Each one of these can be further broken
down so standard foundations we're going to have basically maybe form
work, rebar,
concrete, and then back filling and
beams connecting these different foundations, or pile caps for
piles and things like that. All of these are going to be different
details for each one of these activities.
Another method, which most of you are probably more familiar with is
the master format. The Master format used to be known as 16
divisions in the past, that is what most contractors are familiar
with. And then the construction specifications Institute, or the
CSI, which is the body that developed both the Uniformat and
the master format, came up with a newer format in 2004
instead of the 16 divisions. Now it's anywhere between 48 and 49
divisions. So they broke down these divisions into more details,
and there are some divisions that are still blank, reserved for
further addition, like 3637 3839
there is nothing in there, but something can be added in the
future to this set of specification,
our vehicle to convert the big project into the major tasks until
we reach the level of details, is called the work breakdown
structure, or WBS. This is a very important tool to dissect the
project until we reach the level of work packages, which can be
broken down later on into activities. So a project work
breakdown structure is a deliverable or product oriented
grouping of project work elements showing shown in graphical display
to organize and subdivide the total work scope of the project.
So basically, what we're saying here is that the work breakdown
structure is a graphical translation of the scope of work
of the project. It can be used as a planning tool and as a control
tool as well, to make sure that we did not skip anything or forget
anything in our planning for the project. It is not an activity
listing. It stops one step short, or maybe two steps short of
activity listing. So we stop at what's called a work package,
which later on, can be broken down into activities. And it usually
follows what's called the 15555,
model, which means each entity is going to be broken down into five
sub entities, and each one of these five, in turn, is going to
be broken down in five. And which one of these is going to be broken
down in five until we reach a comfortable level of detail.
Again, it's not yet the activity level of detail one step higher,
which we call the work package.
So the decomposition of the total project work identifies the
deliverables and the related work, and it follows a structure and
organization, which is the WBS decomposes the dub the upper WBS
levels into lower level, detailed components. One becomes five,
developing and assigning identification codes to the WBS
components because we're going to use these for scheduling later on,
or with some modification, we can use them as cost accounts for our
cost accounting for the project. In this case, instead of being
called WBS, it's going to be called CBS, or the cost breakdown
structure similar to that as well. If you can imagine something like
an organization chart that shows at the top the president of the
CEO and the vice presidents, and then the directors and going going
down until you reach the field personnel. This is called an
organizational breakdown structure, or OBS. So these three,
the WBS, the CBS and the OBS.
Us break down one big idea into smaller levels that are even more
manageable and controllable, verifying that the degree of the
composition is
necessary and sufficient. So again, this is a tool for review
and for control, to make sure that everything in the scope of work
has been adequately covered in that work breakdown structure.
The work breakdown structure includes 100% of the work defined
by the project scope and captures all deliverables. It focuses on
deliverables, not activities, as we just mentioned, that's why it
stops at a work package activities can be created based on these work
packages or based on these deliverables.
To show you the flow of that work breakdown structure, we started
with level one house. That's the project that I want to build. I
broke down that house into a following layer. Again, we call it
15555,
but that's not carved in stone. It could be 14736,
and so on, but it's not going to be 120,
100 so it's going to be a gradual transition from one level to
another layer to a third layer, etc. So we have here the site
preparation, footings and foundations, land design, etc.
Framing the footings and foundations going to include
framing, roofing, utilities, etc. So again, you can break down each
one of these levels into further details until we reach a work
package level.
Now we can see here, for example, coding system,
Acme motors expansion. The name is am Acme motors, and then the
automated system is am 01 conveyor system, am 02 office building, am
03 and then you can break that down, design on engineering of the
office building. So it's going to be am o3 1am, o3 four, and so on.
Each one of these can be broken down, so it's going to be am 03401
and so on.
That's another example of how a work breakdown structure is going
to look like.
And we're going to finish here at the end, at the work tasks, which
can be broken down into activities that usually do not show on the
work breakdown structure.
Now from these works, work packages, we're going to break
that them down into activities. And each activity is going to be
represented by a verb and a noun,
installed carpet, paint wall, place or pour concrete and so on.
So there are three typical types of activities, either a
procurement activity, which is purchasing or contracting to get
steel or to get mechanical equipment or to get elevators or
electrical supplies or concrete production, which is the heart of
the construction schedule, placing that concrete and management so
the required submittals, owner or engineer approval, testing and
delays, which are not production or procurement activities, but
they still form major milestones and flags and constraints in the
project, therefore, we need to reflect them on the schedule. We
also have something called milestones, which we mentioned
initially. The project start is a major milestone. The project
completion is a major milestone. The building encloses a milestone.
Substantial completion is a milestone. And so on. These are
zero duration activities. It just shows that this is the separation
between the previous phase and the following phase
flags. We have something called the flag, which is half of a
milestone, start flag or finish flag. So if you look at the
milestone, it can be split to two halves. There's going to be start
Task, start flag, like, for example, the notice to proceed.
Notice to proceed, is going to act as a milestone or as a start flag
for the rest of the project and
completion of submittals. This is going to be a finished flag. There
could be a start flag for the submittals and a completion flag
for the submittals and so on.
Activities should include action related words, as we just said,
words announced, procurement is going to include words like,
fabricate, order, deliver. Production is going to include
install, place, erect, paint, clean, demolish. Management is
going to be submit, approve, Review.
Apply for a payment or for a request for inspection or things
like that.
In addition to descriptions, activities usually have activity
identifications or IDs, as we're going to see in the automated or
the computerized schedule, we're gonna have an activity ID and an
activity description separate from that ID. The IDs can show
locations, trades and work types, etc, etc, if you're if we go back
a couple of slides here, this is an activity ID, am 03, it could
something like that. Basically, this is not an activity, but it
can start. It can be the beginning of an activity. So if we go three
levels below that, it's going to be AM, 0301,
1225,
for example, that could be an activity.
And here's an example, the first four digits are going to be a
serial number for a project and
for example here, this is going to be a
a master format, CSI code, heavyweight, structural concrete.
And then 21 is the placement. And then it could be location
responsibility, and then column number 34 at the end. So each one
of these numbers represents something meaningful, and we're
going to have sort of a dictionary for these activity IDs so that
anyone who doesn't really know can follow the explanation and the
description in that dictionary to understand what this activity
stands for.
Here's another example.
So now that we have broken down the project into activities and
identified each activity, we need to start thinking about the
activity duration. The activity duration one more time is going to
be obtained from our famous equation Q over P. So in practice,
work test duration are determined by one or more of the following
methods. Past experience. Either we have done this activity so many
times in the past, so we can expect how long is it going to
take? Estimates based on Q over P. Order, you have to finish this
activity in five days, or something like that, or use of
predictive models. If we do this activity this way, it's going to
take that many days. If we do it that way, it's going to take that
many days again. It's based on both past experience and
estimates,
and the activity duration can either be deterministic or
probabilistic. Deterministic, which means there's only one
duration for the activity obtained again from the equation Q over p,
but probabilistic is there is some probability that we're not going
to finish in that duration based on the conditions, based on the
performance of the resources based on the availability of resources.
So if we're looking at historical data, we may say we've done this
activity 100 times in the past. 20% of the time it took extremely
long. It took 10 days. 20% of the time it was really done in short
time. It took only four days, but most of the time, in 80% or in 60%
of the previous 100 times that we've done this activity, it took
seven days. So now we have three different durations for the
activity, four, which is the shortest, 10, which is the
longest, and six or seven, which is the most repetitive from past
experience. Which one are we gonna use to schedule the project? Now
remember, this applies to every activity. If you have just 200
activities in the schedule, and you keep adding these different
probabilities, you're gonna end up with the lowest estimate, which is
two months, and the longest estimate, which is 18 months. You
definitely cannot go to the owner and say, Mr. Or Mrs. Owner, we're
gonna finish your project in two months, or maybe in 18 that
definitely is not gonna work. Therefore, we need to factor all
of these probabilities to come up with something meaningful with a
certain level of certainty. And this is basically what we're gonna
discuss in a future lecture called probabilistic scheduling. And
we're going to learn about the technique that we can apply to get
one duration out of these three different durations for each
activity
with the deterministic task duration, the activity may have a
fixed duration or a resource entity is to be captured for a
specific time. So I'm gonna have this excavator available for only
three days. Therefore I need to use it for a certain number of
hours each day to finish that task. I have a fixed amount of
work, and I know the production per hour. So how many hours per
day? How many days? That's how I'm going to estimate.
It the deterministic duration, the activity duration may be subject
to small variations about the specific mean value, so that from
any useful time scale, the work test duration is constant. The
duration, again, is equal to quantity divided by production
rate, Q over P that we have discussed so many times, so fast,
so far. Now when we talk about probabilistic duration
distributions, we're going to talk about this in more details, but
you're going to find that we have something called the mean or the
most likely duration, and we're going to have something called the
optimistic duration, which is the shortest possible, and the
pessimistic duration which is the longest possible. We're going to
see an equation based on statistics. How can we factor all
of these three into one duration for the activity? Basically,
basically converting determine probabilistic into as much
deterministic as possible?
We're going to use something called production table, or
product productivity tables. You can find some of these in the
means book, for example, or in the walker book for estimating. And
definitely, I will always suggest that each company builds its own
production tables, or productivity tables based on its own resources,
whether it subcontractors or equipment or labor or materials,
etc. So the productivity table is going to show you, for example,
that if the masonry unit size is eight inch blocks, with no
conditions, then you can produce up to 400 units per day per Mason.
So knowing what's the total number of units that we need to place, we
can divide it by the number of masons and get the number of days
that's going to be needed and so on. So you can see different
conditions. And if the wall is long, then definitely we're going
to have more production, because you're going to have minimum
interruptions. So we can achieve 430 units per day per Mason. If
the wall is not long, if it's a short wall with corners and a lot
of interruptions and so on, that's going to reduce our production
rate to 370, units per day, per meter. So based on these
productivity tables, we can estimate the duration of the
activity.
This is a quick review of the durations between activity, the
relationships between activities we discussed before the finish to
start, which is the most common relationship, also known as
traditional relationship. And we may add here between the two
activities a positive number that's going to be a lag, or a
negative number that's going to be an overlap. We also have the start
to start relationship where and again, here we can add a lag
between the two activities. It can be with or without lag the finish
to finish. Same thing connects the finishes or the ends of the
activity. It can either have lag or without lag. And the fourth
one, which is the start to finish, as we discussed before, very rare
in its use, and usually it might have either legs or no legs, that
it can go either way
between the activities. Again, we talked about legs and overlap, so
the legs going to be a positive number, whereas the overlap is
going to be a negative number.
So basically, this is a quick introduction about how to build a
schedule. So we're going to see some exercises that we're going to
be working on taking a project, how are we going to break it down
into activities or work packages, and then develop an activity list
based on that, to start our activity list and then add the
sequencing of the activities, add the durations of the activities,
and then calculate our schedule based on the algorithms of the
critical path method. I will see you in the next lecture. You.