Ihab Saad – Concrete and Masonry Operations I
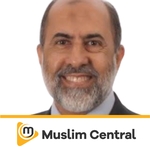
AI: Summary ©
The speakers discuss various hazards that can occur during construction, including violation of guidelines, damage to equipment, and potential hazards such as walls and floors. They stress the importance of limiting access to workers and prevent injuries, and provide examples of hazards such as violation of guidelines, damage to equipment, and potential hazards such as walls and floors. The speakers also discuss control measures for preventing damage and the importance of proper construction and construction equipment to ensure safety. They provide guidance on proper clothing and protection for workers and employees, and plan to resume the presentation in a future video file.
AI: Summary ©
Steve,
hello and welcome to another lecture on integrity, on
construction safety. Today we're going to talk about concrete and
masonry safety. This is a long lecture, so we're going to divide
it into two parts. One part is going to talk about concrete and
the other part is going to talk about masonry. So what do we need
to know about concrete and masonry, a lot of activities take
place in concrete and masonry construction, and these can be
very hazardous if attention and care are not taken into
consideration.
So what are some of the most frequently cited series
violations, failure to protect employees from impalement, which
is basically rebar not being kept or covered, as we're going to talk
about it in a minute. Failure to establish a limited access zone,
to limit the number of workers in the danger zone where a masonry
wall is under construction. We're going to talk about what's a
limited access zone, failure to brace unsupported section of
masonry wall over eight feet in height. When the wall is still
under construction, it's not strong enough yet. So if it's not
properly supported, it can collapse with strong wind or heavy
equipment passing next to it and so on. Failure to have drawings or
plans at the job site to indicate Jack layout and formwork
placement, especially for certain types of concrete operations that
require a lot of coordination, as regard to see on the next slides.
So the first issue is protection from impalement. Impalement,
basically is when something sharp can penetrate the body of a
worker. So what are some effective control measures that can be used
to guard your bar so employees cannot fall into or onto the rebar
and become impaled. We can either prevent the employees from working
in an area where there's they may fall into or onto unprotected
rebar. In some cases, that's not the easiest solution, so we have
to look for other solutions as well. So if this is not possible,
use guard rails or other fall protection measures, as outlined,
as we're going to discuss later in subpart M that deals with fall
protection.
And third, with that second option available, we're going to rebar.
The rebar is going to be capped with special protective rebar
covers, as you can see in the picture, to keep employees from
being impaled. We do not use plastic or paper cups or tape as
rebar cover, as a rebar cover, because they do not protect
workers from impalement. So it has to be sturdy enough, according to
specifications, to prevent even if someone falls on top of it, it
would not be broken or torn and allow for impalement as well. The
rebar also can be banned, but only when an engineer has approved this
practice, or the rebar can be covered with lumber. So if you
have multiple bars next to each other, you can extend a two by
four board, for example, on top of them, and that would prevent the
hazard of impalement
here, as we can see, the mushroom cap, which is the one that shows
here in this picture, this is not allowed because it's ineffective.
The square cap with reinforced
base here at the top is the one that's accepted, and that's the
one that's effective. So here on the next picture, we're going to
see examples of that. So here, for example, we can see that the rebar
here is capped with concrete, small concrete blocks. Here you
can have also a two by four. Here we have these mushroom calves in
some cases, again, as we mentioned, unless they are
reinforced, they're not going to be allowed. Here we have a clear
violation, because you have an opening and it's not showing
whether they're kept or not. So I guess they're not kept. That's an
impairment hazard. So this is a violation.
Here we have the rebar has been bent again, following instructions
from the structural engineer, and here we have either caps or the
two by four covering the rebar. So both of these are acceptable
options.
Another hazard that comes with construction
of concrete work is when we have
post tensioning work for pre stressed concrete, basically for
the pre stressed concrete, you induce stresses in the concrete
tendons, which are the rebar. But concrete tendons tend to have
stress into them. So when you load the concrete element, it
counterbalances these stresses, yielding a smaller size and
lighter in weight concrete element. So for post tensioning
work, the following precautions have to be followed. Access shall
be limited behind the jack to those performing the work. The
jack is going to be used to tension these tendons, signs and
barricades are required to limit access as well, so that people who
are not who should not be working in this area are not going to be
performing any work. So on this.
Slide on the picture here we can see that these are the tendons,
and here they are capped. And here's the jack tensioning these
tensioning these tendons.
So again, we're going to try to limit access within this area to
only people who have to be there. So
a third hazard this area, when it comes to concrete, is concrete
placing. We have multiple ways of concrete placing, whether it's
through a pump, whether it's through buggies, whether it's
through a tower crane and buckets. So here we're going to talk about
tower cranes and buckets. Employees are not allowed to work
under concrete buckets being lowered or elevated into position,
because just in case something goes wrong with the bucket itself
and it opens concrete. Dropping from that bucket can kill someone,
if someone's standing underneath it, and as much as practical,
bucket should be routed to minimize the number of employees
exposed to overhead buckets. So in the design of the operation
itself, we're going to take that into consideration with the motion
of the tower crane and of the buckets. Here on this picture, it
shows multiple people standing next to a concrete bucket. No one
standing underneath it. They opened the chute for that bucket,
and we can see concrete flowing out of the bucket to the place
where it's where it's supposed to be,
another area of hazard also is with concrete mixers with capacity
greater than one cubic yard, they must have a mechanical device to
clear the skip of materials, so that no one would be tempted to go
inside and try to clean that skip. Guard rates should be used on each
should be on each side of the skip again, preventing anyone from
falling in compressed air hoses on concrete pumping systems must have
failed safe connectors, because, again, compressed air at a very
strong force can can cause injuries. Masonry saws must have
semi circular guard enclosure. If you remember, when we talked about
theories of accident causation, we mentioned that improper use of
equipment, this is one of the common ones. People sometimes
remove the guard, thinking that's got to expedite the operation, but
that, again, that's a violation by itself. Do not remove that guard
because it has a protective role and function.
So here we have the guard rails so that no one can fall, and here we
have the guard enclosure around that saw
concrete buggies again, if you are, if someone's pushing that
buggy and they trip, they may be impaled by the impact with the
handles of the buggy. So concrete buggy handles cannot extend past
wheels on either side, to prevent that impalement and prevent anyone
working around again by being affected by it.
Concrete pump poses must have connectors to prevent separation
under load, because again, you may risk having the concrete fall
under pressure from that hose and concrete buckets with hydraulic
release must have a device to prevent accidental dumping, and
that's why, basically, we do not allow people to stand underneath a
concrete bucket while it's being lifted or lowered.
Power concrete travels must have dead man switch. So basically, as
long as they are held by the laborer, by the employee who is
pushing it, they are in operation. As soon as they release their
handle from
from that switch, it stops automatically. So if someone trips
again, the blades of that concrete travel would not cause any
injuries.
Here, what we have is a bull float which has a long handle. Now, the
problem here is that we're working close to power lines and power
equipment which can cause a hazard of electrocution. So the wood
floor handles must be non conductive if electrical contact
is possible. So it can be of a non conductive material, whether wood
or fiberglass or something like that.
Okay, so this is basically talking, in brief, about some of
the hazards that can come with concrete operations. What about
some hazards that can come? Can come with Mason reconstruction
operations as well. So here we're going to talk about the major one,
which is wall collapses, especially when the wall is still
under construction. As we mentioned, the cut, the mortar has
not set yet, so the wall has not gained its permanent strength yet.
Therefore it needs to be supported or protected from collapse. What
are some of the effective control measures that can be used to
eliminate the hazard of being in danger in the danger zone, to
protect employees from being struck by flying brick or block in
the event of a wall collapse, so until the wall.
Has gained sufficient strength
that overturning is no longer a hazard. Overturning again, which
is sort of a collapse due to strong wind or
vibration around it, keep employees out of the area where
the wall is being constructed unless they are actually engaged
in constructing the wall. Of course, if they are engaged in
constructing the wall, they have to be in close proximity to it.
But if once the wall is complete, until it gains its strength, then
no one should be close to it, working close to it, the most
effective control measure is to follow the standard by marking off
an area with tape, rope or chain or any other material that will
indicate to employees that they are not to enter that zone or area
that has been marked. This is what we call limited access zone. In
this case, only the Masons who are working on constructing that wall
are going to be allowed in this area. Out of that marked area,
people can work, but inside it only the masonry crew that's
working on constructing this wall, the zone should be equal to the
length of the wall under construction and extend out a
distance equal to the height of the wall to be constructed, plus
four feet, because again, if it collapses, debris is going to fly
everywhere. So you're adding four feet of buffer zone beyond the
height of the wall. So if the wall, for example, is eight feet,
then that horizontal extent is going to be 12 feet. If the wall
to be constructed is 10 feet high and 30 feet long, the zone is
going to be 14 feet
by 30 feet, which is the length of the wall.
If a wall is over eight feet in height. What are some of the ways
to brace a wall over eight feet to provide protection against the
hazard of collapse, the project engineer or competent person
should determine how best to brace the wall. According to the
magazine of masonry construction, a typical masonry wall brace
includes a vertical member, an inclined strut, stakes, and, if
necessary, a brace. We're going to see a picture that illustrates
this concept. What kind of material is going to be used for
the support scaffold planks, two by 10s are typically used as the
vertical member and the inclined strut, and two by fours for stakes
and strut braces, two by fours and two by sixes are considered by
most expert to be inadequate for vertical member or inclined
struts. That's why we're using the scaffold planks. All lumber must
be in serviceable conditions. So it must be in good condition, not
rotting or not suffering from any damage. The American National
Standards Institute, which is called NC, has a standard for
concrete and masonry work, which is NCA one, 10.9 1983
recommends that the support for bracing, the support or brazing,
shall be designed by or under the supervision of a qualified person
to withstand a minimum of 15 pounds per square foot. Remember
that number, 15 pounds per square foot. Local environmental
conditions such as strong wind, for example, need to be considered
in determining the bracing design. Braces or shores should be secured
in position to prevent them from moving, thus losing this their
effectiveness,
if you're going to be placing concrete inside that wall, in this
case, tremies, which is the hose that's going to be used to convey
that concrete must be secured with wire rope or equivalent, to
prevent them from moving. And again, concrete might start
spreading around, Lockout and tag out is required for work on
equipment used for concrete and masonry. If they are defective,
they need to be locked out or tagged out, so no one would use
them until they are being properly maintained or repaired.
So here we have the picture of a tremie
that's being used to convey the concrete. In this case, we are
using a conveyor belt to drive the concrete to the place and then it
falls through the tremie to try to minimize the scattering and
sputtering of concrete all around
forecast in place, concrete, which is also called Concrete test in
situ. Formwork must be designed, fabricated, erected, supported,
braced and maintained, so that it will be capable of supporting
without failure all vertical and lateral loads. That's why, for
example, we have a code for not removing the formwork until a
certain number of days have passed after placing the concrete is
determined by the quality of the concrete, by the weather, by the
span, by the design and so on. Several factors involved in the
duration before we can remove the formwork drawings or plans and any
revisions for Jack layout formwork, etc, must be available
at the job site, especially if we have.
Certain types of concrete being placed, like slip form, for
example, or lift slab. We're going to talk about that in a moment.
We must also include four more scaffolding and any shoring
equipment in these drawings, so they have to show the spacing, for
example, between the different elements of the scaffold and the
props and so on. To
give you an example of how hazardous this operation can be,
there's a very famous sad accident in Willow island in West Virginia
on april 1978
51 workers were killed in the collapse of scaffolding used to
pour concrete for a cooling tower under construction, 45 workers
fell more than 150 feet, and six were crushed to death on the
ground. So basically we're talking about the scaffolding itself
collapsed. There was the weight of the concrete, there was the weight
of the people on top of it, the weight of rebar. It could not
support all of that weight. So there's the static weight of the
formwork and the rebar, and the dynamic load by the people walking
on top of it, and the dynamic load of the concrete being placed, all
of that resulted in the collapse of the formwork. And as you can
see, a very large number of people lost their lives.
Here. We can see, for example, an example of shoring. Shoring is to
be inspected prior to erection, before and after and during
concrete placement, to make sure that it's still in a good
condition supporting the load of the concrete placed on top of it.
Reshoring also needs to be inspected. So after you remove the
formwork, the bulk of the formwork, and you keep a few
props, these have to be inspected on a regular basis to make sure
that they're doing their job.
These are the concrete. That's a picture of samples of concrete
taking into cylinders. That's going to be tested on a regular
basis, as you remember from your materials class, is going to be
tested after seven days, and it's going to be tested again after 28
days to determine whether this concrete complies with the
expected compressive strength or not. So that's why a random sample
is going to be taken every certain number of cubic yards of concrete
to be placed, we're going to take a sample, and they're going to be
kept in good conditions, according to the standards, until they are
tested again, whether after seven days or after 28 days,
when you are placing concrete on site. Damage, shoring is not to be
used because, again, it loses its efficiency and effectiveness, and
therefore it should not be used. Shoring that's found to be damaged
must be immediately reinforced. The sills for shoring must be
sound rigid and capable to carry the maximum intended load. The
sills are going to be used to distribute the load. Instead of
being a point load is going to be a larger area. Load just the same
idea of a footing underneath a column. For example,
all base plates, Shore heads, extension devices and adjustment
screws must be in firm contact with the foundation and the form
and secured when necessary to make sure that they do not move from
place under the pressure of the concrete on top of them.
In case you have eccentric loading, which means it's not
axial loading on top of the prop on top of the shore head.
Eccentric loads on shore heads are not allowed unless designed for
this, because this creates, in addition of the load itself, it
creates a moment which may overturn that shore head. It means
loads not centered on the head. Lateral loads can cause failures
because of that, unless the shoring is properly designed to
take these lateral loads.
So for example, here on this slide, we can see that we have
some lateral loads from this this cantilever. So that's why we have
this diagonal or these slanted shoring as additional support for
the formwork,
also with casting face concrete whenever single posture post
shores are tiered, which means, if you have, for example, the the
floor height is 12 feet, and you have only eight foot long shores,
and they're going to be tiered. Which are which means are going to
be sliced.
Additional requirements to be followed are that the short must
be designed and inspected by a qualified person, vertically
aligned, properly aligned, spliced to prevent misalignment, and
braced in two directions at splice levels and in each tier. So all of
these are precautions so that they do not collapse or deform a.
A
shoring and reshoring are not to be removed until concrete strength
is sufficient to support its weight and any other imposed
loads, as we mentioned before, that's going to be dictated by
code. The code is going to tell you exactly how long it should
take before removing the formal because if you remove it too soon,
even if the concrete does not collapse. It might sag and cause
permanent deformation in the structure, which can lead to
weakness later on, leading to collapse. Adjustment of single
post shoring not to be made after placement of concrete, because,
again, you are now changing the load distribution. Reshoring to be
erected as original shoring is removed as needed for support. So
after a certain number of days, we're going to have less demand on
the number of shores that we have. So we're going to start removing
them gradually. And these shores are going to be recycled or
removed or reused for a different floor on top of the one, we're
working on
four more stripping, which is removing the formwork after the
concrete has been placed, has to be an organized and coordinated
operation. What we can see on this slide, although it appears as if
it were a collapse, this was supposed to be properly
synchronized and designed, but it seems that at least one
shore one prop was removed too soon, which resulted in the
collapse of the formwork on two separate floors. That should not
happen, because the falling debris can injure and or maybe even kill
people, although the concrete itself is safe. But again, the
removal of the formwork in this case, was the crop. So
and here we have the use of a spotter, and we have a restricted
access area because of the falling debris, again, we don't want it to
cause any injuries to anyone.
Slip forms, I don't know how familiar you are with slip forms.
But for example, if you have seen the construction of an elevated
water tank or the core of a high rise building, a concrete core of
a high rise building, usually the method that we use for that is
what's called a slip form, which means the form is going to be on
both sides of the wall and it's going to be jacked up very
gradually, very slowly, while concrete is being placed at a
certain rate that allows concrete to strengthen while the forms are
being lifted up. So scaffolds or work platforms are required for
slip forms. Design must be adequate and self safe. Rate of
lifting must not be exceeded. That rate of lifting is going to be
really slow. It's going to be a few inches an hour, maybe so to
allow concrete to gain enough strength before you remove that
formwork, so that synchronization has to be studied and properly
calculated.
Another hazard in concrete comes with the reinforcing steel.
Before, we have talked about the vertical rebar and the hazard of
impalement and we talked about how to cover the rebar, we also have
the horizontal rebar that's used for slabs. For example, rolls of
reinforcing wire shall be anchored to prevent recoiling, because if
they come in rolls, they have already gained that shape of a
cylinder. So if you try to to straighten them, they would tend
to recoil again if they are not properly angled.
Sometimes this rebar would come in sheets, not in in in coils. And in
this case, it's going to be much easier to install reinforcing
steel for walls, columns, etc, should be adequately supported to
prevent overturning, because, again, if it overturns, first of
all, it can injure someone. And second, if you place the concrete
without the rebar, then it's not a reinforced concrete wall, and can
lead to a collapse.
Another hazard of dealing with concrete is the lung exposure to
concrete itself its effect on the skin, which is which can cause a
skin this is called dermatitis. So contacting dermatitis from
concrete exposure can cause severe burns to skin and eyes. Therefore,
we're talking about gloves. We're talking about boots and preferably
long sleeve shirts and long long pants, not shorts, definitely to
cover as much skin as we can have and try to eliminate any
unnecessary exposure to concrete.
So the best practice is employees should wear full length trousers,
long sleeve shirts, rubber boots and gloves to avoid prolonged
contact with concrete. Not mandatory. But this is a good
practice. So if you are a safety supervisor or if you are a field
engineer responsible for any concrete work, try to follow this
best practice.
Also, employees exposed to a concrete splatter should wear eye
protection because that can hurt the eyes, and in case of.
An injury from particles from concrete while pulling or placing
it. Washing facilities and I wash solution should be provided.
Again. This is not mandatory, but definitely this is good practice.
And as we mentioned before, you care about your employees. You
want them to be safe, so we're going to follow that best
practice. Let's pause here, and then we're going to resume this
presentation in another video file. I.